Things we can do for you
We do this
Plastic injection mouldings and assembly, supported by a full project engineering function. We take programs from CAD models to mass production, supporting the customer throughout.
WE EXCEL AT THIS
Liaising with our tool makers we use Mouldflow analysis to ensure optimum tool and part design before making a tool, to reduce the risk of correction loops.
WE DO THIS AS WELL
Logistic, storage and packaging solutions. We utilise modern technology from EDI to A.S.N., including barcode verification process allowing unique traceability to the customer.
OUR SUPPORT IS THE BEST
Our customers rely upon us to ensure a smooth product introduction – Service is a huge part of what we do! That is why we develop relationships with the customers. Team work is paramount to our success.
Experience
Our Engineering team have extensive knowledge and experience within the plastics and automotive industry and work very closely with customers to develop the product to match or exceed their expectations.
Project Management
A first class project management service from initial concept with the customer right through to SOP, ensuring all customer specifics and milestones are achieved in a controlled and cost-effective process against tight lead-times.
Services
Labone excel in providing IATF 16949 2016 certified procedures which can be applied at any stage of a project depending on customer requirements. We will provide weekly review meetings with detailed timing plans, progress reports and on-site customer support for all trial builds whether in the UK or overseas
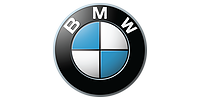
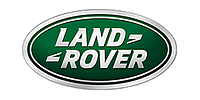
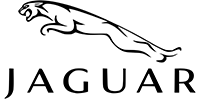
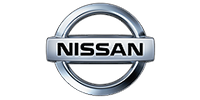

33 Machines
The plant list covers 33 machines spanning a tonnage range from 50T to 1080T. In addition, a wide range of assembly stations unique to customer requirements are established with full fault prevention auto checking.
Quality Parts
An extensive range of materials are processed and controlled within established protocol. New procedures are constantly being added as we continue to meet the ever changing market place and the need for more visual high-quality parts.
24 Hour Operation
Working a 5 day 24 hour operation with 3 shift cover the maximum time is allocated to schedule achievement through effective schedule control and change over optimisation.
Over 30 Machines
The plant list covers over 30 machines spanning a tonnage range from 50T to 1080T. In addition, a wide range of assembly stations unique to customer requirements are established with full fault prevention auto checking.
Quality Parts
An extensive range of materials are processed and controlled within established protocol. New procedures are constantly being added as we continue to meet the ever changing market place and the need for more visual high-quality parts.
24 Hour Operation
Working a 5 day 24 hour operation with 3 shift cover the maximum time is allocated to schedule achievement through effective schedule control and change over optimisation.
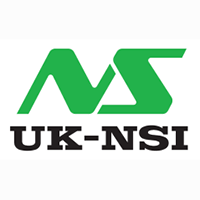
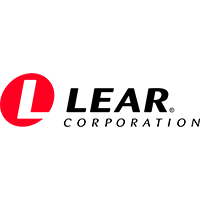
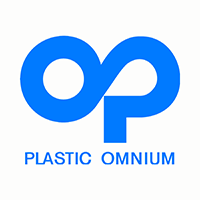
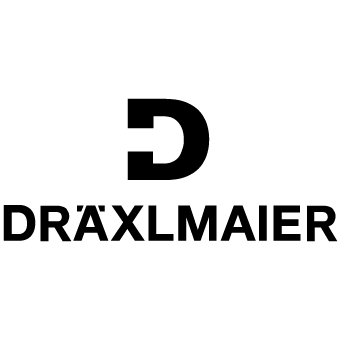
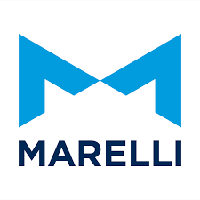
Product Approval Process
We always strive to work closely with our customer and supply base to achieve product excellence. Our product approval process (1st off, last off and in-process audits) ensures we meet all customer requirements.
Continuous Monitoring
We monitor and control key elements of the product through SPC, gap and flush, CMM measurements, Colour matching, in-process gloss controls and other measurements tools.
Team Approach
We always take a team-based approach in all problem-solving tasks using a number of quality tools such as 8D, Fishbone analysis, 5 Why’s, QRQC, Cap studies, MSA and PFMEA.
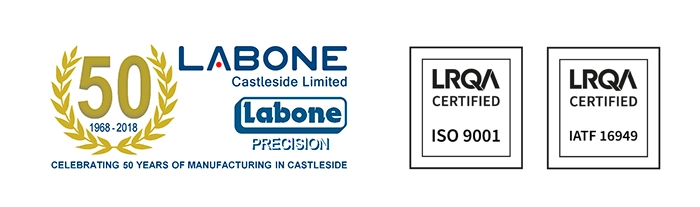